Table of Contents:-
- What is Work Measurement?
- Define Work Measurement
- Work Measurement Objectives
- Procedure of Work Measurement
- Components of Work Measurement
- Advantages of Work Measurement
What is Work Measurement?
Work measurement is concerned with the time it takes to complete a task assigned to a specific job. Work Measurement is a term which covers several different ways of finding out how long a career or part of a job should take to complete. It can be defined as the systematic determination, through various techniques, of the amount of adequate physical and mental work in terms of work units in a specified task. The work units are usually given in standard minutes or standard hours.
Define Work Measurement
According to the British Standard Institution, “work study is the application of techniques designed to establish the time for a qualified worker to carry out a specified job at a defined level of performance”.
Work measurement goes hand in hand with method design. At the same time, the method design is directed towards studying the components of a single or multiple operation of a system. It is a technique by which the actual time consumed in operating is computed and ultimately serves as a suitable time standard. Work measurement is the study of the work content of a job to lay down a fair day’s work. It seeks to provide a quantitative assessment of the human work in a specified position and to establish the proper time for adequate job performance.
Work Measurement Objectives
The objectives of work measurement are given as follows:
1) To determine the standard cost and as an aid in preparing budget.
2) To balance the team activities of those jobs that require several workers.
3) To determine schedule and planning work.
4) To determine the effectiveness of the machine.
5) To balance production lines for new product or new models.
6) To prepare cost estimates of new products.
7) To establish supervisory objectives and provide a basis for measuring efficiency.
8) To determine time standards to provide a basis for wage incentives plans.
9) To determine time standards to provide a basis for labour cost control.
Procedure of Work Measurement
The basic procedure to be followed sequentially for work measurement are as follows:
Step 1: Select the work to be studied after having made a preliminary survey.
Step 2:Â Record all the relevant data about the circumstances in which the work is being done, the methods used, and the activity elements involved.
Step 3:Â Measure each element in time over a sufficient number of activity cycles to ensure a representative picture has been obtained.
Step 4:Â Examine the recorded data and critical time elements to ensure that unproductive or random elements are separated from productive parts; also, examine the recorded time and determine a representative time for the cache feature.
Step 5:Â Compile a time element for the operation, which will provide a realistic standard of performance and will include time allowances to cover suitable rest, personal needs, contingencies, etc.
Step 6:Â Define precisely the series of activities and method of operation for which the time has been allowed and issue the standard time for the actions and procedures specified.
Components of Work Measurement
Work measurement components are classified into performance rating, allowance, standard time and synthetic time standards.
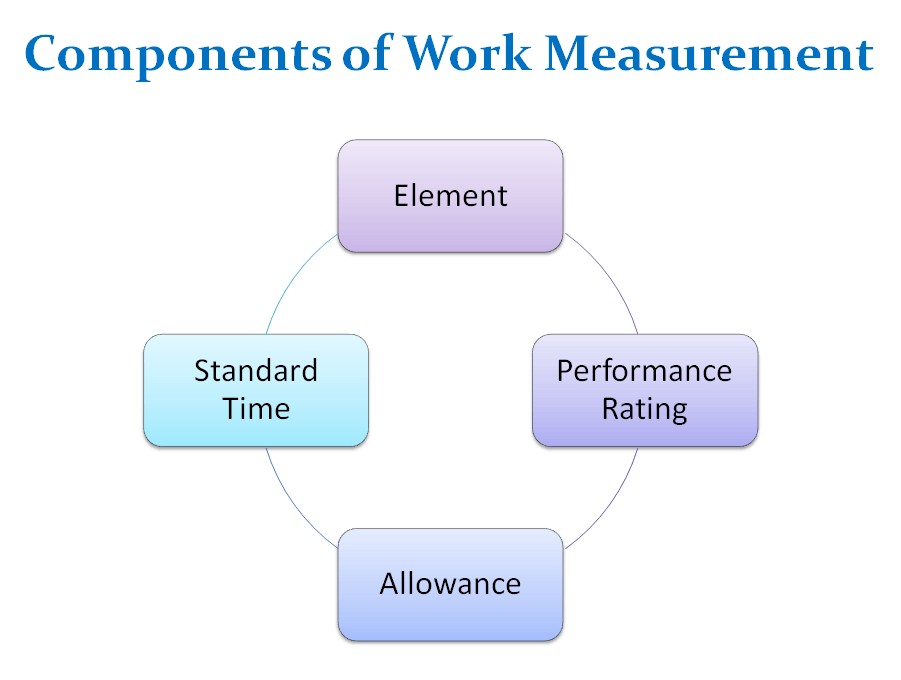
Components of Work Measurement are listed below:
- Element
- Performance Rating
- Allowance
- Standard Time
Element
An element is a distinct part of a specified job selected for measurement, observation, and analysis convenience. The various types of factors involved in a job are as follows:
1) Repetitive Element: It occurs in every work cycle of the job. For example, it picks up a component from the container before assembly operation.
2) Occasional Element: It occurs at intervals, for example, when setting a tool on a machine.
3) Constant Element: For which the primary or average time remains constant whenever it is performed, for example, measuring a dimension.
4) Variable Element: For which the primary or average time varies.
5) Manual Element: This is performed manually.
6) Machine Element: This is performed automatically by a machine.
7) Governing Element: It occupies longer than any other element in a job.
8) Foreign Element: It is found to be an unnecessary element of a job, for example, unexpected tool breakage.
Performance Rating
Not all operators operate at the same pace. Therefore, it would be unfair to establish a standard for work performance solely based on the time taken by either a fast or a slow operator.
Some speed allowance, therefore, must be made in the time values obtained through time study for the pace at which the operator performs the task. Determining the relative speed or tempo of an operator’s work is known as the rating.
Rating the speed of the union operator is a matter of judgment for the tiny study analyst. This is one of the aspects of time study that has been considered the main focus of the time study analyst. A more precise measure of an employee’s performance would be subjective. Although most devise any means that would overcome rely on the analyst’s judgment.
- Performance Rating = Observed Performance/ Standard Performance * 100
Allowance
A worker cannot work with the same efficiency throughout the shift or working day as after some hours of work, he gets tired. As he continues to work in the change of the day, he suffers from fatigue from the work undertaken and the conditions under which he works. The time taken to complete the task dramatically depends on the working conditions.
Standard Time
The time taken by a qualified worker to perform a particular operation is referred to as standard time. Work measurement is the application of specific techniques to determine the degree and quantity of labour used in performing tasks. The time consumed by an average worker, working at an average speed, to perform a specific task under normal working conditions is generally referred to as work standard, time standard, or simply standard. It is expressed in terms of time elapsed per unit of output or units of production per unit of time. Managers use these standards in controlling, planning, and scheduling their operations. Therefore, work measurement estimates the worker time required to produce one unit of a specific output.
Standard Rating is defined as the output rate which qualified workers will naturally achieve as an average output for a given period. This rating is denoted as 100.
Computation of Standard Time
Standard time is represented by the formula:
Standard time = Normal time + Allowances
Normal or Basic time = Observed time x Rating factor
Normal or Basic time = Observed time x Observed rating / Standard rating
Several readings are taken for each element, depending on the degree of accuracy desired and the length of the work cycle. The average observed time of each component is calculated by dividing the total of the element times by the number of processes for which the element times are recorded.
Advantages of Work Measurement
The advantages of work measurement are as follows:
1) It serves as a basis for methods analysis by comparing the efficiency of alternative work methods. Other conditions being the same, the method requiring minimum time will be the test method.
2) Work measurement enables the preparation of realistic work schedules through accurate assessment of human work about plant capacity for production and maintenance planning.
3) It helps balance the work of different workers so that each task takes equal time to perform.
4) Work measurement provides an objective basis for wage incentive plans by setting machine utilization and labour performance standards.
5) It provides information on which estimates for tenders, selling prices and delivery schedules may be prepared.
6) It facilitates workforce planning by comparing actual time with standard time. Estimates for future labour requirements and costs can be prepared. It serves as a basis for labour budgeting and budgetary control systems.